Papers with Whittle Lab authors at ASME Turbo Expo, 11-15 June 2012, Copenhagen

Origins and Structure of Spike-Type Rotating Stall
G. Pullan, A.M. Young, I.J. Day, E.M. Greitzer, Z.S. Spakovszky
Paper GT2012-68707; Session 40-2; Wednesday 2:30pm-5:30pm
In this paper we describe the structures that produce a spike-type route to rotating stall and explain the physical mechanism for their formation. The descriptions and explanations are based on numerical simulations, complemented and corroborated by experiments. It is found that spikes are caused by a loss of pressure rise capability in the rotor tip region, due to flow separation resulting from high incidence. The separation gives rise to shedding of vorticity from the leading edge and the consequent formation of vortices that span between the suction surface and the casing. As seen in the rotor frame of reference, near the casing the vortex convects toward the pressure surface of the adjacent blade. The approach of the vortex to the adjacent blade triggers a separation on that blade so the structure propagates. The above sequence of events constitutes a spike. The simulations show shed vortices over a range of tip clearances including zero. The implication is that they are not part of the tip clearance vortex, in accord with recent experimental findings. Evidence is presented for the existence of these vortex structures immediately prior to spike-type stall and, more strongly, for their causal connection with spike-type stall inception. Data from several compressors are shown to reproduce the pressure and velocity signature of the spike-type stall inception seen in the simulations.
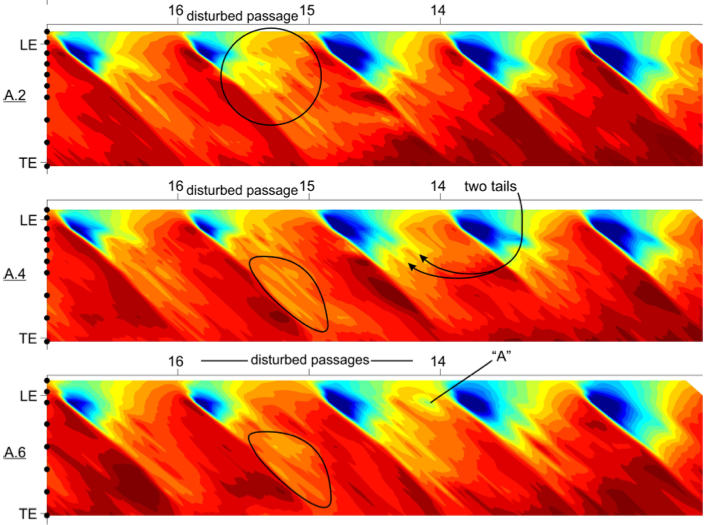
Detailed Measurements of Spike Formation in an Axial Compressor
S. Weichert and I.J. Day
Paper GT2012-68627; Session 40-2; Wednesday 2:30pm-5:30pm
This paper presents new experimental measurements of spike-type stall inception. The measurements were carried out in the single stage Deverson compressor at the Whittle Laboratory. The primary objective was to characterize the flow field in the tip clearance gap during stall inception using sufficient instrumen- tation to give high spatial and temporal resolution. Measure- ments were recorded using arrays of unsteady pressure trans- ducers over the rotor tips and hot-wires in the tip gap. Pre-stall ensemble averaged velocity and pressure maps were obtained as well as pressure contours of the stall event. In order to study the transient inception process in greater detail, vector maps were built up from hundreds of stalling events using a triggering sys- tem based on the stalling event itself. The results show an embry- onic disturbance starting within the blade passage and leading to the formation of a clear spike. The origins of the spike and its relation to the tip leakage vortex are discussed. It has also been shown that before stall the flow in the blade passage which is most likely to stall is generally more unsteady, from revolution to revolution, than the other passages in the annulus.
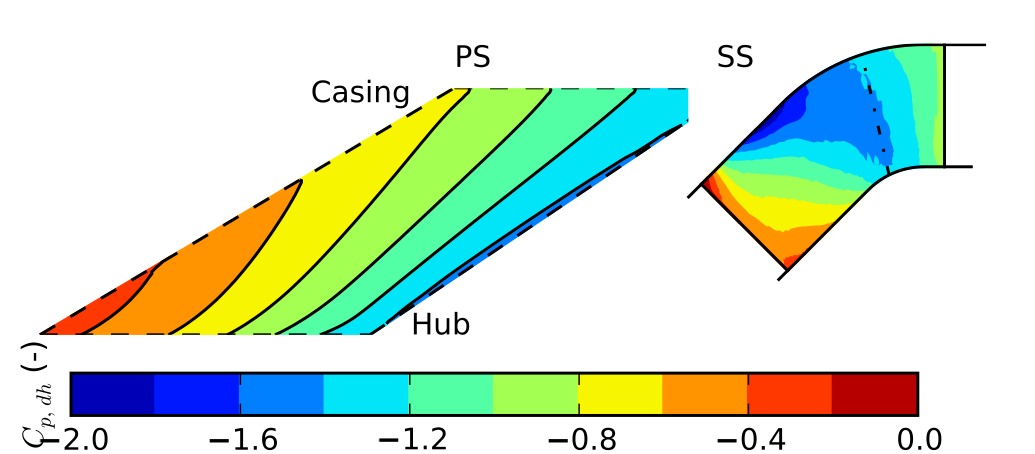
Aerodynamic Design of High Endwall Angle Turbine Stage, Part 1: Methodology Development
A.W. Cranstone, G. Pullan, E.M. Curtis and S. Bather
Paper GT2012-68705; Session 34-4; Wednesday 10:15am-12:45pm
A design methodology is presented for turbines in an annulus with high endwall angles. Such stages occur where large radial offsets between the stage inlet and stage out- let are required, for example in the first stage of modern low pressure turbines, and are becoming more prevalent as bypass ratios increase. The turbine vanes operate within s-shaped ducts which result in meridional curvature being of a similar magnitude to the blade-to-blade curvature. Through a systematic series of idealised computational cases, the importance of two aspects of vane design are shown. First, the region of peak endwall meridional curvature is best located with the vane row. Second, the vane should be leant so as to minimise spanwise variations in surface pressure - this condition is termed -F!ideal lean". This design philosophy is applied to the first stage of a low pressure turbine with high endwall angles.
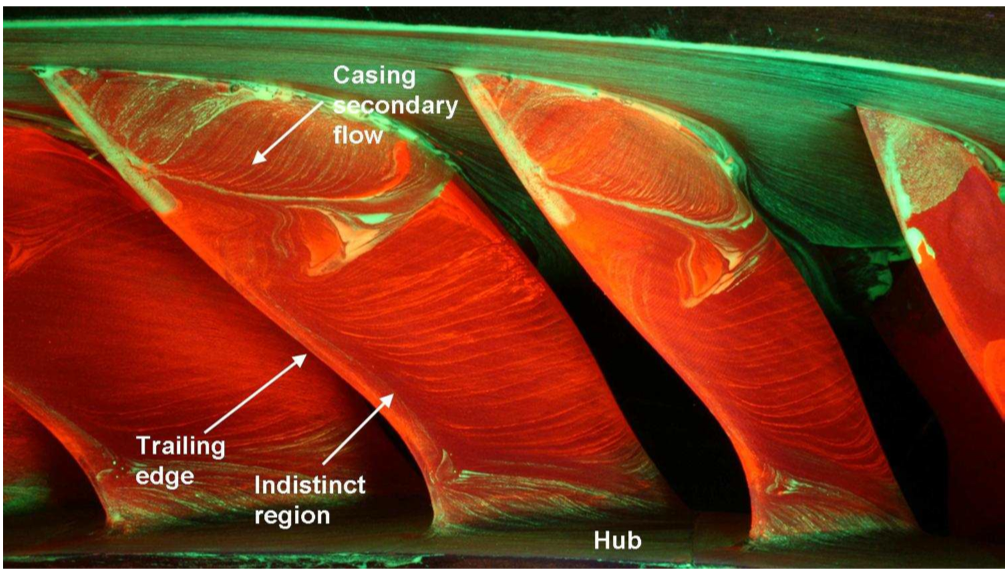
Aerodynamic Design of High Endwall Angle Turbine Stage, Part 2: Experimental Varification
A.W. Cranstone, G. Pullan, E.M. Curtis and S. Bather
Paper GT2011-68706; Session 34-4; Wednesday 10:15am-12:45pm
An experimental investigation of a turbine stage featuring very high endwall angles is presented. The initial tur- bine design did not achieve a satisfactory performance and the difference between the design predictions and the test results was traced to a large separated region on the rear suction-surface. To improve the agreement between CFD and experiment, it was found necessary to modify the turbulence modelling employed. The modified CFD code was then used to redesign the vane, and the changes made are described. When tested, the performance of the redesigned vane was found to have much closer agreement with the predictions than the initial vane. Finally, the flowfield and performance of the redesigned stage are compared to a similar turbine, designed to perform the same duty, which lies in an annulus of moderate endwall angles. A reduction in stage efficiency of at least 2.4% was estimated for the very high endwall angle design.

A Numerical Investigation into the Sources of Endwall Loss in Axial Flow Turbines
J.D. Denton and G. Pullan
Paper GT2012-69173; Session 34-4; Wednesday 10:15am-12:45pm
Endwall loss, often termed secondary loss-A!, in axial turbines has been intensively studied for many years, despite this the physical origin of much of the loss is not really understood. This lack of understanding is a serious impediment to our ability to predict the loss and to the development of methods for reducing it. This paper aims to study the origins of the loss by interrogating the results from detailed and validated CFD calculations. The calculation method is first validated by comparing its predictions to detailed measurements in a turbine cascade. Very good agreement between the calculations and the measurements is obtained. The solution is then examined in detail to highlight the sources of entropy generation in the cascade, several different sources of loss are found to be significant.
The same blade row is then used to study the effects of the of the inlet boundary layer thickness on the loss. It is found that only the inlet boundary layer loss and the mixing loss vary greatly with inlet boundary layer thickness. Finally a complete 50% reaction stage, with identical stator and rotor blade profiles, is examined using both steady calculations, with a mixing plane model, and the time average of unsteady calculations. It is found that the endwall flow in the rotor is completely different from that in the stator. Because of this it is considered that results from endwall flow and loss measurements in cascades are of limited relevance to the endwall flow in a real turbine. The results are also used to discuss the validity of the mixing plane model.
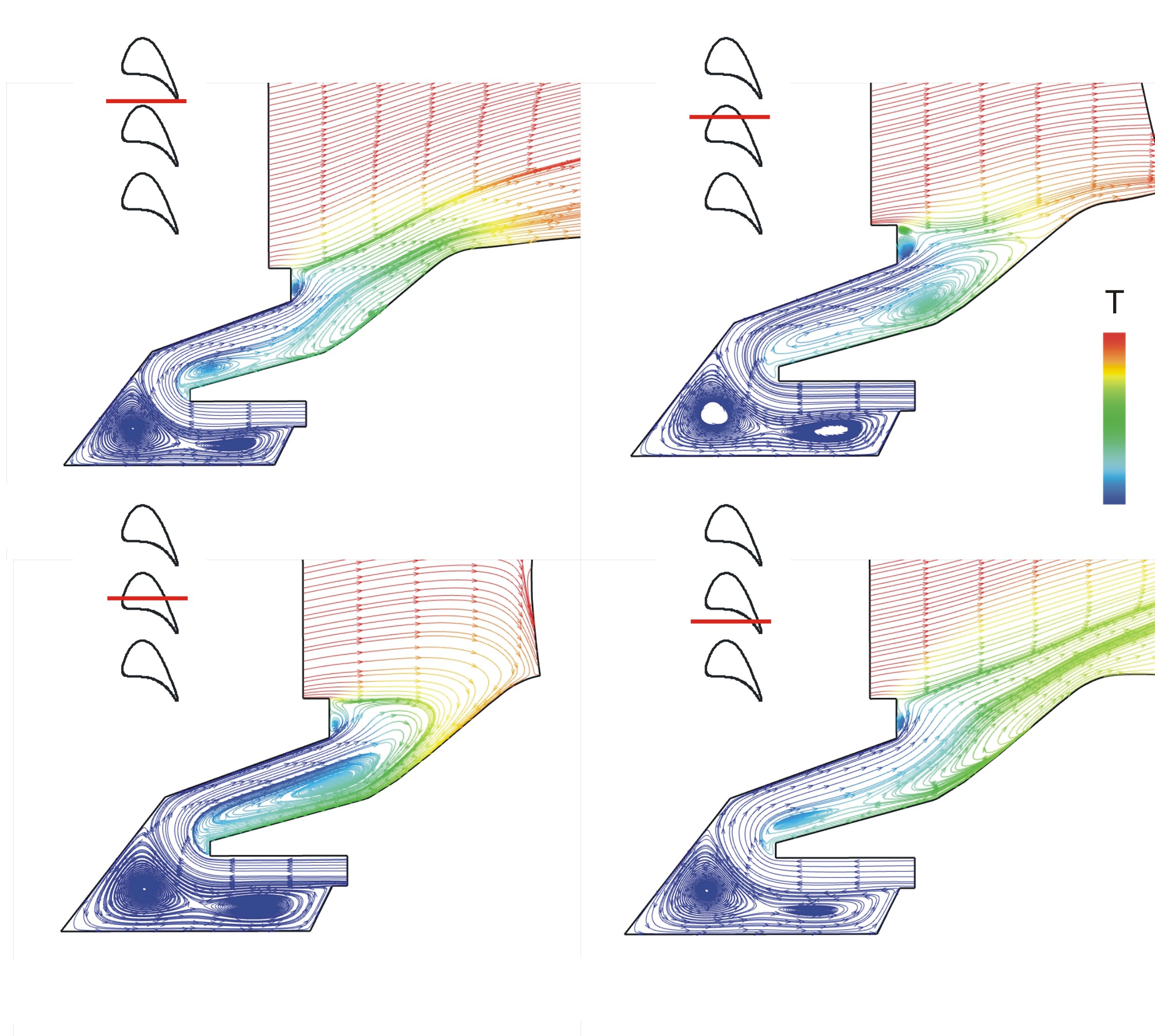
Unsteady Interaction between Annulus and Turbine Rim Seal Flows
M. Chilla, H.P. Hodson and D. Newman
Paper GT2012-69089; Session 34-5; Wednesday 2:30pm-5:30pm
In core gas turbines relatively cold air is purged through the hub gap between stator and rotor in order to seal the disc space against flow ingestion from the main annulus. Although the sealing mass flow rate is commonly very small compared to the main annulus mass flow rate, it can have significant effects on the development of the passage endwall flows and on the overall loss generation.
In this paper, the interaction between annulus and rim sealing flows is investigated using numerical simulations of a generic high-pressure turbine. At first, the numerical approach is validated by comparing the results of calculations to measurement data at the design flow conditions. Following that, results from steady and unsteady calculations are used to describe in detail the aerodynamics in overlap-type rim seals and their effects on the blade passage flow. It is found that the flow interaction at the rim seal interface is strongly influenced by the velocity deficit of the rim sealing flow relative to the annulus flow as well as by the circumferentially non-uniform pressure field imposed by the rotor blades. At typical sealing flow conditions, the flow interaction is found to be naturally unsteady, with periodical vortex shedding into the rotor passage. Finally, the influence of the specific rim seal shape on the flow unsteadiness at the rim seal interface is investigated and the impact on turbine performance is assessed.
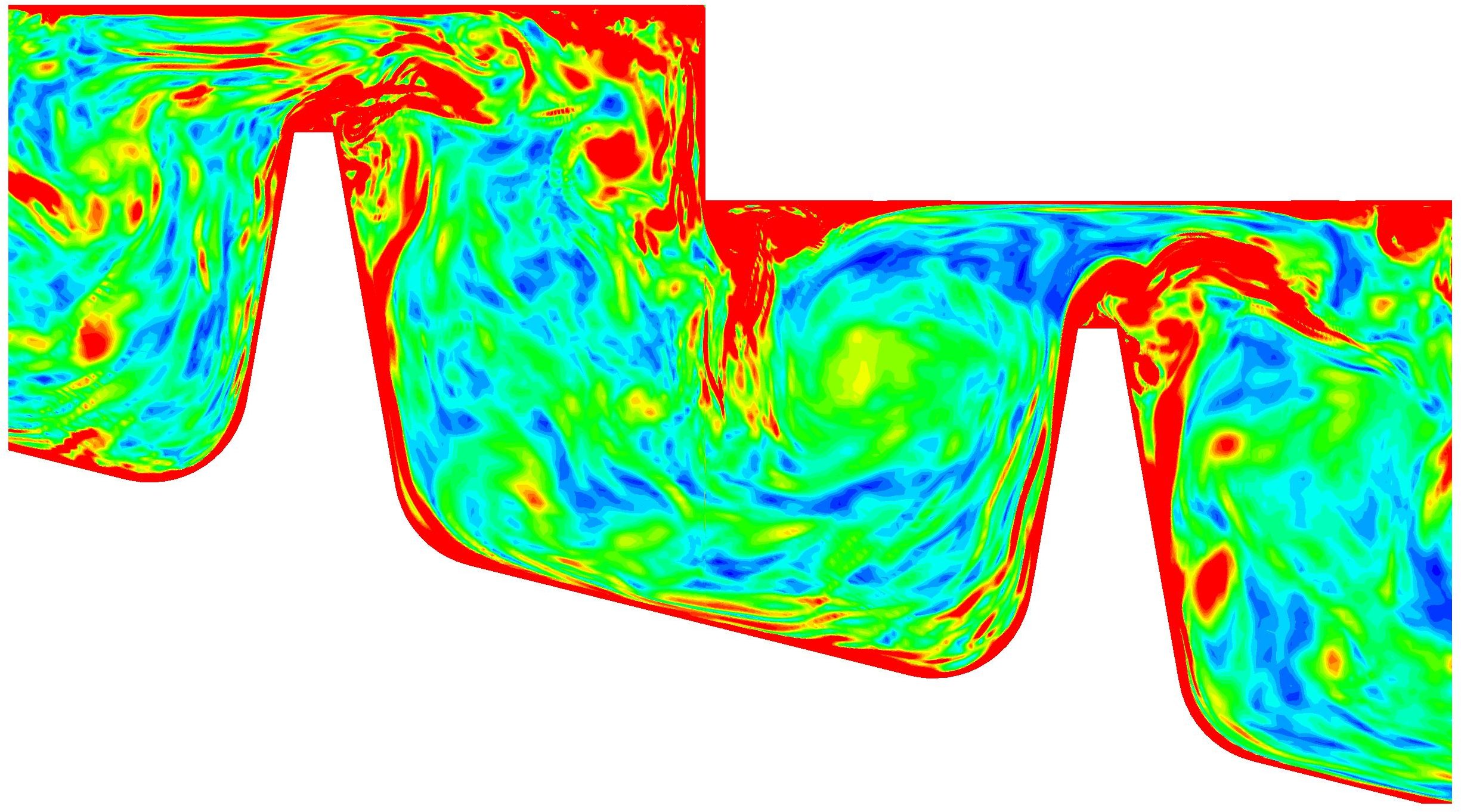
On LES Methods Applied to Seal Geometries
J. Tyacke, R. Jefferson-Loveday and P.G. Tucker
Paper GT2012-68840; Session 35-4; Thursday 8:00am-10:00am
Nine Large Eddy Simulation (LES) methods are used to simulate flow through two labyrinth seal geometries and are compared with a wide range of Reynolds-Averaged Navier-Stokes (RANS) solutions. These involve one-equation, two-equation and Reynolds Stress RANS models. Also applied are linear and nonlinear pure LES models, hybrid RANS-Numerical-LES (RANS-NLES) and Numerical-LES (NLES). RANS is found to have a maximum error and a scatter of 20%. A similar level of scatter is also found among the same turbulence model implemented in different codes. In a design context, this makes RANS unusable as a final solution. Results show that LES and RANS-NLES is capable of accurately predicting flow behaviour of two seals with a scatter of less than 5%. The complex flow physics gives rise to both laminar and turbulent zones making most LES models inappropriate. Nonetheless, this is found to have minimal tangible results impact. In accord with experimental observations, the ability of LES to find multiple solutions due to solution non-uniqueness is also observed.
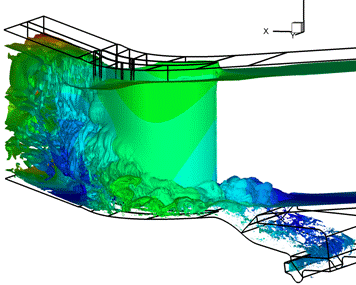
Implementation and Assessmenet of an Advanced Plenum Boundary Condition for Turbine Design Calculations
R. Jefferson-Loveday, P.G. Tucker and J. Northall
Paper GT2012-68090; Session 35-8; Wednesday 2:30pm-5:30pm
In an effort to provide predictions for hot annulus ingestion flows across turbine rim-seals and shroud cavity interfaces, this paper describes a new plenum boundary condition based on characteristic boundary methods that has been formulated and implemented into the Rolls-Royce in-house CFD solver HYDRA. It is assessed for a rim-seal on a 1.5 stage research turbine at two different operating points and seal mass flow rates. For shroud cavities it is tested on a recent engine geometry design at realistic operating conditions. Downstream total pressure loss profiles show a significant improvement for the rim seal and encouraging improvement for the shroud cavity geometry when compared with the original HYDRA boundary conditions. The improvement is assessed through examination of flow fields at the cavity/mainstream interface. The observed flows show improved agreement with the fully meshed cavity test-cases.
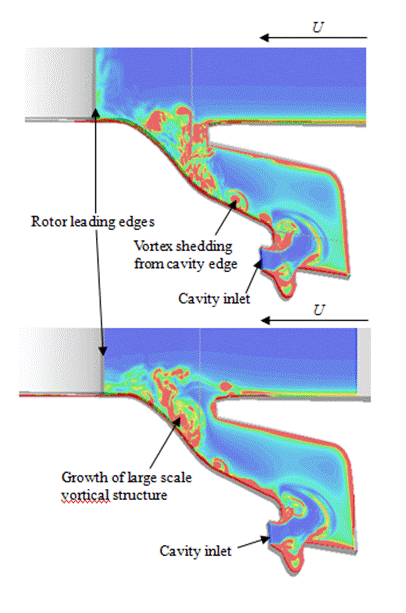
Implementation and Assessmenet of an Advanced Plenum Boundary Condition for Turbine Design Calculations
R. Jefferson-Loveday, P.G. Tucker, V.N. Rao and J. Northall
Paper GT2012-68091; Session 35-6; Thursday 2:30pm-5:30pm
A Hamilton-Jacobi differential equation is used to naturally and smoothly (via Dirichlet boundary conditions) set turbulence length scales in separated flow regions based on traditional expected length scales. Such zones occur for example in rim-seals. The approach is investigated using two test cases, flow over a cylinder at a Reynolds number of 140,000 and flow over a rectangular cavity at a Reynolds number of 50,000. The Nee-Kovasznay turbulence model is investigated using this approach.
Predicted drag coefficients for the cylinder test-case show significant (15%) improvement over standard steady RANS and are comparable with URANS results. The mean flow-field also shows a significant improvement over URANS. The error in re-attachment length is improved by 180% compared with the steady RANS model. The wake velocity profile at a location downstream shows improvement and the URANS profile is inaccurate in comparison.
For the cavity case the HJ-NK approach is generally comparable with the other RANS models for measured velocity profiles. Predicted drag coefficients are compared with large eddy simulation. The new approach shows a 20-30 % improvement in predicted drag coefficients compared with standard one and two equation RANS models. The shape of the recirculation region within the cavity is also much improved.
The Sensitivty of 2D Compressor Incidence Range to In-Service Geometric Variation
M.N. Goodhand, R.J. Miller and H.W. Lung
Paper GT2012-68633; Session 33-9; Tuesday 10:15am-12:45pm
The loss mechanisms which control 2D incidence range are discussed with an emphasis on determining when real in-service geometric variations will have a large impact. For the majority of engine compressor blades (Minlet>0.55) these loss mechanisms, at both negative and positive incidence, arise due to the presence of supersonic patches. It is shown that these patches are highly sensitive to the geometric variations close to, and around the leading edge. The variations used in this study were measured from newly manufactured as well as ex-service blades. Over most the high pressure compressor considered the manufacture variations were found to dominate. Despite large geometric variations (~10% of leading edge thickness), only small, consistent reductions in mean incidence range were observed over much of the design space. The exception to this was for very sharp leading edges where a rapid drop in positive incidence range was observed. The mechanism for this is reported and design guidelines for its avoidance offered. In the final part of the paper, the consistent behavior at negative incidence and the transonic nature of the flow is exploited in order to design a robust asymmetric leading edge with a 5% increase in incidence range.